HazCom training requirements simplified, we believe "Safety Should Be Simple"
The Hazard Communication (HazCom) standard consistently ranks among OSHA's Top 10 infractions year after year, making it the most-cited standard in General Industry. Despite its importance, employers often struggle with compliance, particularly when it comes to training requirements.
Who requires to be trained and when?
All employees should be supplied with details and training on harmful chemicals in their workspace at the time of their preliminary project (prior to being exposed to a chemical), and whenever a new chemical hazard they have not previously been trained about is presented into their workspace. For example, if employees have actually been trained to deal with corrosives, but a brand-new chemical is an oxidizer, they would require training on that hazard.
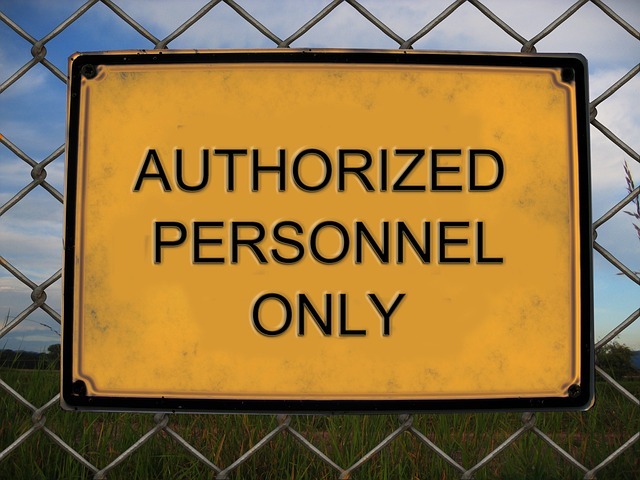
The guidelines enable you to create details and training to cover classifications of hazards, such as flammability or carcinogenicity, or particular chemicals.
Chemical-specific details must constantly be offered through labels and Safety Data Sheets (SDSs).
What requires to be covered in training?
Employees must be warned of any operations in their workspace where harmful chemicals exist, and the area and accessibility of the composed hazard interaction program, including the required list(s) of hazardous chemicals, and SDSs.
Training must include a minimum of:
Approaches and observations that might be utilized to find the presence or release of a dangerous chemical, such as monitoring carried out by the employer, continuous tracking devices, visual appearance or smell of dangerous chemicals when being released, and so on;
The physical, health, simple asphyxiation, combustible dust, and pyrophoric gas hazards, as well as threats not otherwise classified, of the chemicals in the workspace;
How employees can safeguard themselves from these hazards, including specific procedures in location to safeguard employees from direct exposure to dangerous chemicals, such as work practices, emergency procedures, and personal protective devices (PPE) to be utilized; and
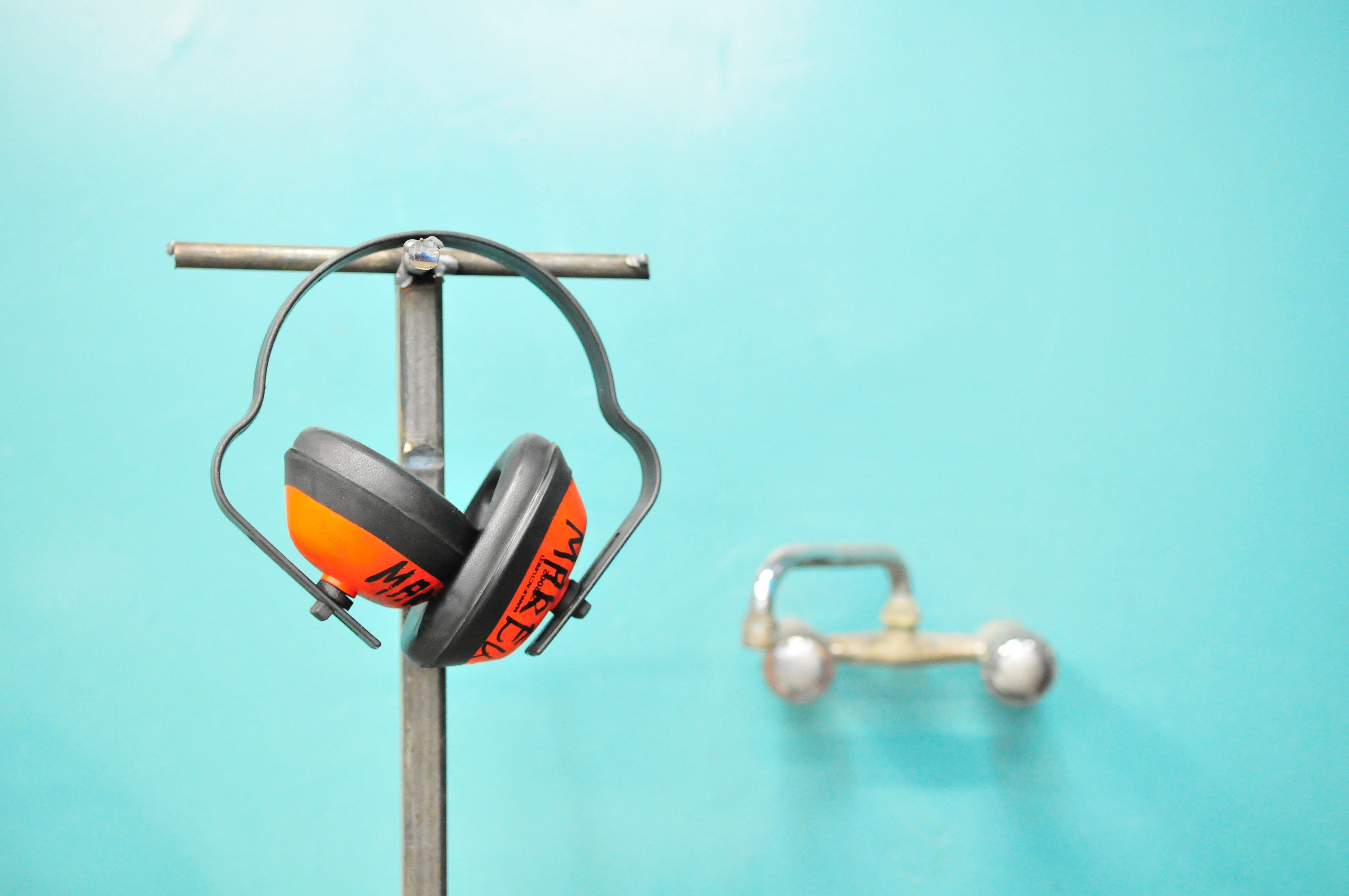
The details of the risk communication program, consisting of an explanation of the labels gotten on delivered containers and the workplace labeling system utilized by their company; and the SDS, including the order of details and how employees can acquire and utilize the proper threat details.
What does that actually mean?
"Training should cover the following basics:
1. Ways to detect the presence or release of hazardous chemicals, such as employer-conducted monitoring, visual inspection, or recognition of chemical smells.
2. The various hazards posed by chemicals in the workplace, including physical, health, asphyxiation, combustible dust, pyrophoric gas, and other unclassified threats.
3.Measures employees can take to protect themselves from these hazards, including established work practices, emergency protocols, and the proper use of personal protective equipment (PPE)."
Is refresher training required?
After initial Hazard Communication (HazCom) training has been completed, there are rules and regulations for retraining employees to ensure ongoing compliance and safety. These regulations are outlined by the Occupational Safety and Health Administration (OSHA) and may vary depending on the specific circumstances of the workplace and the hazards present.
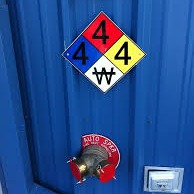
Some specific examples of when retraining may be required include:
1. Changes in Hazardous Chemicals or Processes: If new hazardous chemicals are introduced into the workplace or there are changes in processes that could affect employees' exposure to chemicals, retraining is necessary. For example, if a new chemical is added to the inventory or if there are updates to Safety Data Sheets (SDS), employees must be trained on the new hazards and safe handling procedures.
2. Employee Job Changes or Transfers: When employees change roles or transfer to new departments where they may be exposed to different hazardous chemicals or processes, retraining is necessary to ensure they understand the hazards associated with their new job tasks.
3. Safety Incidents or Near Misses: If there is a safety incident, near miss, or exposure to a hazardous chemical in the workplace, retraining may be required to reinforce safety protocols and prevent future incidents.
4. Annual Refresher Training: Some employers choose to provide annual refresher training to all employees as a proactive measure to reinforce HazCom requirements, refresh employees' knowledge, and keep them informed about any updates or changes in regulations.
5. Employee Requests or Feedback: If employees express concerns or request additional training on specific topics related to Hazard Communication, employers should consider providing retraining to address their needs and ensure their safety.
It's important for employers to regularly assess their HazCom training programs and identify opportunities for retraining to address any gaps in knowledge or changes in workplace conditions.
Retaining copies of training.
After initial Hazard Communication (HazCom) training has been completed, there are rules and regulations for retaining records to ensure ongoing compliance. Employers are required to maintain documentation of HazCom training for each employee for a specified period.
Specific examples of record retention requirements include:
1. Training Records: Employers must keep records of initial HazCom training provided to employees, including the date of training, topics covered, and names of trainers. These records should be kept for the duration of the employee's employment.
2. Safety Data Sheets (SDS): Employers must ensure that Safety Data Sheets (SDS) for hazardous chemicals used in the workplace are readily accessible to employees. These SDS must be retained for as long as the chemical is present in the workplace.
3. Written Hazard Communication Program: Employers are required to develop and maintain a written Hazard Communication program that outlines the procedures for communicating chemical hazards to employees. This program, along with any updates or revisions, should be retained for the duration of employment and for 30 years thereafter.
4. Chemical Inventory: Employers must maintain an inventory of hazardous chemicals present in the workplace. This inventory, along with any updates or revisions, should be retained for as long as the chemical is present in the workplace.
5. Employee Training Records: Employers must retain records of refresher or additional training provided to employees, including the date of training, topics covered, and names of trainers. These records should be kept for the duration of the employee's employment.
Failure to retain these records as required by OSHA regulations can result in citations and penalties during inspections.
It's essential for employers to maintain accurate and up-to-date records to demonstrate compliance with HazCom requirements and ensure the safety of their employees.
Write A Comment